
Sean Dornan
E-mail: seandornan@hotmail.co.uk
Phone: +44 (0) 7979474676 (UK)
Languages Spoken: English
Curriculum Vitae

Professional info
I have predominantly worked within the Oil & Gas Industry for the last 32 years with most of my career in the pipeline coatings sector. In the last 10 years I have branched out to subsea structures & other fabrication including design, fabrication & installation of pipeline welding facilities which has included double & quad jointing facilities.
I am considered a reliable & component Individual by my colleagues and peers having proven my knowledge & performance working in some very difficult & challenging projects around the world. I have developed many long-term professional relationships within industry having supported each other through difficult projects & situations. With only a few exceptions, my projects come about by word of mouth from senior officers of my clients, recommending my services to their networks who were seeking a reliable & professional person to undertake their projects.
I also a have good knowledge base as a fitter/ fabricator, engineering & coating inspector. I have a strong HSE & Quality background working at the forefront of the industry with projects for the top tier companies with very demanding standards of operation. I am a Nace level 2 coating inspector with extensive knowledge of laboratory & field testing, application systems, operational procedures & industry standards.
I am confident that my range of skills in surface preparation, pipeline coatings, project management & coating inspection will meet your needs. Please also look at the comments my clients have left below in the recommendations section.
-
Concrete Weight Coating (Impingement and Wrap-on)
-
Multi Layer Polypropylene Blown Foam insulation Coating including Injection Moulding
-
Polyurethane Insulation Coatings.
-
Internal and External paint Coatings
-
FBE Anti-Corrosion Coatings for internal and external applications
-
3 Layer Polypropylene and Polyethylene Coatings
-
Asphalt Enamel and Coal tar Coatings
-
Field joint coatings
Other areas of Expertise:
-
Project Management
-
Pipeline coating site operations Manager & Superintendent
-
Procurement: Equipment Selection, Price negotiation & Purchase
-
Research & Development
-
Q/A Q/C site lead
-
Surface Preparation
-
Logistics
-
On the job training
-
Project Planning & Bid Preparation
-
Site, Facility & Equipment mobilisation & commissioning
-
Maintenance Manager & technician
-
Inspection & Testing of Coatings
-
Mechanical fitter & Fabricator
-
Plastic Extrusion Technician – Design, installation & refurbishment
-
Anode and Doubler pad installation
Professional Qualifications, Certification & Training
High/Secondary School: Mathematics, English, Mix Sciences, Technical Drawing, Wood and metal working
Computer literacy: Excel, Word, Microsoft Project, Smart Draw, Basic AutoCAD, Basic PowerPoint.
Nace Level 2 Coating inspector: #62425 31-10-2027
Offshore Medical: Re-qualify upon clients request
BOSET, HUET and EBS: Re-qualify upon clients request
MIST: Re-qualify upon clients request
Norwegian Escape Chute: Re-qualify upon clients request
• Time Served Mechanical Fitter and Fabricator
• Contractor Management
• Crosby Quality Education System
• Permit to work systems
• Control of Substances Hazardous to Health (COSHH)
• Advanced Safety Auditing
• Risk Assessment and Safe Work Procedure
• Facility/Site Superintendent
• Financial and budgeting skills
• Site Supervisor
• Mobilisation and Commissioning Superintendent/ Supervisor
• IOSH Managing Safety
• Incident & Injury Free
• H & S legislative awareness
• Manual handling
• SCAT Incident investigation
• Confined space entry
• Supervisors/due diligence course
• Slinging & Signalling
• Environmental Awareness
• Fire Fighting Equipment
• Leadership skills
• Lock out-Tag out authorized person
• Presentation skills
Work experience

Wasco (Greece), July 2019 to July 2019:
Coating engineer and application specialist.
-
Assess current Wrap-on concrete coating application issues and make any corrections necessary to ensure all production rates and client quality requirements are meet in line with the project requirements.
-
Advise on corrective and preventive actions for the next planned change over.
Achievements:
-
Successfully isolated and corrected the concrete wrap-on coating application issues.
-
Production quality now exceeds customer requirements.
-
Production through put requirement has been exceeded for the current project with all client specifications meet.
-
Trained the operations personnel in the findings and how the corrective actions were implemented to prevent future reoccurrence.
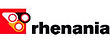
A.Hak Group (Rhenania), January 2019 to June 2019:
General Manager, Coating engineer and application specialist.
-
Assume responsibility for the management and operation of the Rhenania coating facility in Nijmegen.
-
Assess the current status of the coating facility and management teams, advise and create an action plan to correct all current issues to increase profitability.
-
Key responsibility was developing the management and production teams to produce good quality product at the maximum allowable production rate.
-
Train the Rhenania supervisor’s and operating personnel on the correct use and set up of the equipment to reduce re-work and reject rates.
Achievements:
-
Restructured were necessary the management and operation teams to give a more productive overall team with clear roles and responsibilities, which increased the overall performance and profitability of each project.
-
Reduction in the rework and reject rates through on the job training and overall equipment capability awareness.
-
Introduced new bid and project management tactics and tools, which increased overall profits.
-
Successfully completed the transition period and hand over to the new General Manager and Managing Director.
-
Increased customer satisfaction with greatly improved positive feed back from the customer project management teams.
-
All projects were completed on time and to customer specifications with good customer satisfaction.


CPW and Wasco Greece, (Noble, Williams and Baltic connector Projects), 15 Nov 2017 to December 2018:
Wrap-on Concrete coating specialist. Operations Manager. Research and Development Manager.
-
Working initially solely for CPW my role was to assess the current status of the coating facility and its equipment at the Wasco coating facility at the CPW yard in Thisvi Greece.
-
My role developed into CPW supplying my services to Wasco as their operations manager and coatings engineer to assist them in the improvement and development of the facility.
-
Key responsibility was developing the Wasco Wrap-on concrete facility in Thisvi to produce good quality product at the maximum allowable production rate.
-
Train the Wasco and local personnel on the correct use and set up of the equipment.
Achievements:
-
Modified the application unit to produce a smooth and uniform concrete coating, which exceeds the customer’s requirements, with core strength of 40 mpa after just 3 days.
-
Together with Wasco management and TKPS engineers we modified and installed a new incoming system to be able to cope with the increased production rates
-
Re-engineered and modified the coating line which included installing additional equipment to improve the product quality.
-
Reduced the average repair rate from 35% to 2%.
-
Reduced the reject rate to .03%. (With no rejects for 5 weeks being their current record)
-
Increased the production rate from 6.83/hr to 21.46/hr (314% increase)
-
Training and guidance of the local supervisors and coating staff, which can now operate the facility affectively.
-
CPW and Wasco have now completed three projects with complete customer satisfaction in the concrete weight coating facility at Thisvi. All project were delivered on time and to specification.

BrederoShaw, (STT) South of Texas Tuxpan Project, 5 June 2017 to 27 Oct 2017:
Wrap-on Concrete coating specialist for Concrete Pipeline Coating Systems (Tampico wrap-on Concrete Coating Facility, Mexico)
Key Roles and Responsibilities:
-
The Operations & Maintenance Support Specialist is responsible for assisting and advising the Operation and Maintenance managers on how to best optimise the throughput and maintenance program to avoid downtime of the two Heavy wrap concrete coating facilities whilst running a 24hrs per day 6 days per week campaign.
-
Assist and advise with the development of the preventive maintenance programs and training of the local maintenance manager in strategic maintenance planning along with personnel structuring.
-
Troubleshoot the current breakdowns and equipment faults to prevent future reoccurrence.
-
Assist the managers create affective key personnel training requirements.
Achievements:
-
We managed to increase the daily throughput average by 15 pipes per day due to changing behaviour and team cooperation of the production and maintenance teams.
-
Together with the maintenance manager we re-structured the maintenance teams to be more effective and allocated area of responsibilities so the teams were clear as to their daily duties.
-
Over several weeks we developed confidence in the team leaders to take responsibility for their areas and to develop and implement their preventive maintenance rather then reactive.
BP Global Projects, Shah Deniz 2 Project: May 2016 to April 2017:
Insulation & Coating Specialist for Subsea Anti-Corrosion, Thermal Insulation and Concrete Pipeline Coating Systems Inspector (Kabil Coating Facility, Batam Island, Indonesia)
Inspector Key Roles and Responsibilities:
-
The Insulation & Coating Specialist is responsible for executing activities and coordinating specialist inspection resources to implement the project Quality Management System requirements for the Shah Deniz Phase 2 Project, Subsea Line-pipe Coating Works
Quality Management:
-
Provides guidance, advice and training to project team, contractors, suppliers, inspectors and third parties as required to ensure understanding of the project Quality objectives.
-
Acting as Site lead as and when required.
Quality Assurance:
-
Review the contractor’s Inspection & Test Plans and other relevant quality documentation.
-
Identify risks in the contractor’s and sub-contractors which may lead to audits being required to be carried out by the project Quality Specialists / Quality Manager.
Quality Control:
-
Ensures company inspection, surveillance and witnessing of constructed components is executed in accordance with approved ITP’s.
-
Facilitate the project activities to handle contractor queries, non-conformances, deviations and concession requests.
HSE:
-
Re-enforce BP golden rules on contractor’s sites and proactively participate in BP and contractors HSE programs.
Conline Pipeline Coating Services: Dec 2014 to Dec 2015
Coatings Engineer & Application specialist, Engineering & Process Consultant
Management:
-
Working with the site team I was responsible for highlighting the equipment requirements and changes required for the existing facility to produce multi layer coating. Ensure all the changes to equipment were carried out as per agreement and installed correctly for the coatings application process. My responsibility also included over seeing all coating operations for the 5-layer PPF/ FBE and 3 layer coating systems runs and train the local team in how to best set up the facility which included fault finding/ corrections.
Quality and inspection:
-
Generate new procedures which covers all aspects of the 5 layer coating operations, Prepare the Inspection and test plans for 5-layer PPF and FBE coatings for the Moerdijk coating facility. Over see all coating activity to ensure compliance with procedures and industry standards. Witness and monitor all of the sample preparations and testing.

Wasco: Aug 2013 to Aug 2013
Coating engineer – Facility assessment with recommendation.
-
Assess the new Concrete coating facility in Mo I Rana Norway and prepare a list of observations and recommendations based on findings.
PIH: Aug 2013 to Aug 2013
Coating Engineer – Design a custom coating PQT and testing facility.
-
Working directly for the Director of Operations my remit was design a purpose built research and development facility with multiple firing lines with the capability of preforming any Client Pre-Qualification Testing. Facility design to include all pipe handling equipment, client reception and meeting rooms, two multi purpose firing lines visible from the client observation deck, utilisation of existing equipment were possible.
BSR: Dec 2007 to Mar 2013
Coating Engineer - Engineering & Process Improvement.
Client PQT and First production run: July 2011 to Aug 2011
-
Oversee the coating facility set up and production of 4-layer polypropylene blow foam run including all quality control testing. Observe and provide on the job training to the operations personnel.
Equipment Installation: 2009 to 2010
-
Oversee installation of coating conveyor sections for the 4-layer polypropylene PQT.
Equipment:
-
Removal of 160 mm bore plastic extrusion screw and assessment of Barrel and screws. Assess screw profile; make recommendations for fabrication of purpose built polypropylene blown foam screw. Modify existing coating equipment to perform in-house PQT for production of Polypropylene blown foam coating onto 12.75 inch pipe @ 30mm thickness. Oversee and ensure that all required calibrations to the existing coating equipment to are carried out and the required certification is obtained. Perform any material trials required with the existing 160mm plastic extruder to produce .700 density Polypropylene blown foam. Oversee the PQT activities and answer any of the Lloyds representative questions regarding the technical aspects of the operations. Assist BSR management with their expenditure proposals for the upgrading of the current facility and to assist with the selections and technical requirements for any new equipment requests and to review any/ all equipment quotation received. Attend any meetings with senior Corus personnel and directors as required, to answer any technical or process questions arising from the expenditure proposal.
Quality:
-
Oversee the factory and laboratory testing. Report on all findings. Evaluate findings and advice on corrective actions. Oversee coating sample extraction and report on all findings. Monitor and record all coating parameters during the Polypropylene foam application PQT, create findings and recommendations report.
Management:
-
Generate safe work procedure for removal and installation of the 160 mm extruder screw. Generate spread sheet/ calculate required speeds and settings for 4-layer polypropylene blown foam coating equipment. Determine boundaries of existing equipment, highlight when they are crossed. Train existing personnel on set up of facilities coating equipment.
Equipment and Facility assessment: 2007 to 2008
-
Assessment of plastic extrusion equipment and its capability for producing Polypropylene blown Foam; current facility setup and potential production requirements for Polypropylene blown pipe coating; Running material trials to determine the current Plastic Extrusion equipment’s capability of producing Polypropylene foam and conformation with BSR through put requirements; water quenching equipment and coating conveyor setup; Cleaning brush set up, determine required up-grades to produce required cut back configuration for 4-layer coatings; Assess pipe handling and storage equipment for it suitability for handling 4 layer coated pipe; Assess laboratory equipment and advice on the required equipment to perform all required laboratory testing. i.e. Density, tensile strength etc
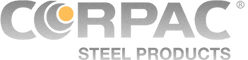
CorPac: Mar 2011 to July 2010
Engineering/ Coating engineer - Engineering & Process Improvement.
-
Provide engineering and technical support for the purchase of a FBE and 3-layer coating facility. Visit suppliers to discuss quotations’ and technical queries. Provide support to project team in the price negotiations and purchase agreement.
Serimax: Jan 2010 to Dec 2010
Project Manager - Engineering & Process Improvement.
Design, Procurement and Project manage the installation of a double jointing and field jointing facility in Malaysia
-
Management: Responsible for redesign of quad jointing facility into double jointing facility. Prepare and negotiate costs and time scale for management and Capex approval. Oversee all engineering and development of required pipe handling equipment based on client’s specification and project requirement. Project manager for all aspects of the fabrication and assembly of the pipe handling equipment. Generate the installation schedule including fabrication and shipping of new equipment. Oversee facility installation.
-
Quality and inspection: Generate equipment specification for tender. Visit Contractor site for approval and selection. Oversee equipment fabrication in accordance with project requirements. Review the existing equipment manuals and generation of new equipment manuals.
Turn Key Pipeline Services:
Coatings Engineer/ Application Specialist, Engineering & Process Consultant
-
Health and Safety: Assessment of the Health and Safety documentation required for the mobilisation of external pipe coating equipment into an existing facility in Russia which included the generation of documentation for Risk assessment of all the proposed works; Method statement generation based on the risk levels; and Installation plan and schedule development
-
Quality and inspection: Review of the existing equipment manuals and correction of all content to suit the Russian requirements including generation of any new equipment manuals.
-
Management: Oversee and assist the Engineering team with the development of the required pipe coating equipment based on the client’s specification and existing equipment. Projects manage all of the fabrication and assembly of the pipe-handling units, spiral pipe coating conveyor and automatic plastic extruder application unit. Generation of the installation schedule based upon the fabrication and shipping of the new equipment. Oversee the generation of all required documentations and manuals to satisfy the Russian regulations and customer requirement.
Welspun Tubular USA:
Coatings Engineer/ Application Specialist/ Engineering/ Process improvement
-
Health and Safety: Evaluate pipe coating facility from HSE prospective; generate action plan, correct non-conformities. Assist and advise local HSE team, instigating and implementing corrective actions. Review H&S management manuals, including American Federal and State HSE requirements. Establish HSE legal compliances for the operation of Pipe coating facility (USA), ensure HSE Management system compliant with requirements. Advise and guide local HSE team to implement HSE management system at site level, including compliance with ISO9001, 14001 and 18000 systems.
-
Quality and inspection: Review of Proposed Quality Acceptance Plan, ensure they met Canadian Standards for Application of Powder Coatings before submission for client approval. Evaluate in house pre qualifications trails of the 36” spiral welded pipe with fusion bonded epoxy coating trails; report back with any recommendations. Witness and report back with recommendations on House test sample panels. Attend site meetings regarding the Trans Canada Project, compile recommendations for compliance with Trans Canada Project specifications.
-
Management: Evaluation of fusion bonded epoxy-coating system, provide a list of improvements and implement. Generate short-term improvements schedule based on retraining the current staff to improve the product through put and Quality. Evaluate FBE coating facility and its equipment, show bottlenecks and provide solutions and upgrades. Risk assessment of project exposure; give payback time and annual profit increase. Evaluate site staff, analysis of their current position, skills and knowledge level. Assist local management with corrective action required.
Corus Tubes:
Coatings Engineer/ Application Specialist/ Onsite Coatings Inspector
-
Quality and inspection: Attend pre qualification meetings, assist with coating based issues. Witness all FBE, Internal and Concrete PQT Coating activities and laboratory testing and report. Perform duties required for the production run and testing of the FBE, Internal and Concrete coatings and report on a daily basis with findings.
-
Management: Ensure all management procedures are adhered to for each product type, report on deviation from agreed procedures. Ensure all health and safety requirements are strictly adhered to during all coating activities and report on all deviations.

BrederoPrice (1989 – 2006)
Oct 2004 – to May 2006. External Coating Facilities, Leith Edinburgh.
Asst Superintendent/Site Superintendent from Feb 2005
-
HSE: Legal compliance of all operations Inc. assessment and generation of procedures and associated training e.g. risk assessments, manual handling, COSHH, certification of Overhead crane operators, FLT operators etc. Execution of required HSE key performance indicators e.g. housekeeping inspections, safety meetings, close out of non-conformances/near misses, incident investigations, production training requirements etc, implementation of the HSE Management system at site level, including compliance with ISO14001 system. Selection and recruitment of sub-contractors and suppliers through risk assessment/ method statement evaluation and management to project completion. Legal compliance of work place equipment e.g. lifting equipment, lifting tackle, cooling tower sampling, pressure vessel testing etc. Implementation of Health and Safety drive to change work place behaviour and work ethics. Membership of site safety leadership team to further enhance Health and Safety of the working environment and key processes.
-
Quality: Client liaison during all operations. Review of Quality procedures and Client specification documentation. Inspection coordination inc - Inspection of incoming materials, recording of material batch numbers, monitoring material storage areas, application process monitoring. Ensure all coating activities are monitored and 100% inspection is carried out during processes Inc. pre-blast/ blasted surfaces, inspection of applied coatings for correct thickness and visible defects, final holiday detection. Witness and final acceptance of coating repairs, clearing of non-conformances. Troubleshooting coating and equipment defects. Witness pre-qualification testing and mechanical testing. Quality of coatings and compliance with ISO9000 systems. Ensure laboratory/field equipment calibrated and fit for use. Participate in project kick-off meetings, review sub-contractor non-conformance reports and technical queries. Technical review of bids. Completion of five year zero defect for Concrete coating compressive strength and impact testing at Leith Concrete coating facility. Successful management and completion of pre-qualification testing for Balgzand to Bacton project, including the first ever 120mm concrete thickness application onto 36” diameter pipe with a pre manufactured steel cage at a rate of 27 p/hr (450 tonnes of concrete) on a single pass through the application unit.
-
Management and coordination: Responsible for all coating/production operations at Leith external coating facilities and management of 250+ personnel. Responsibilities included: Planning, scheduling and management of coating operations, manpower, materials usage/ordering, overtime requirements and to ensure operating facilities are on time and on budget. Generation and management of action plans. Leading operational meetings with Supervision and implementing/managing action plans. Generation of production progress reports, daily expenditures, manpower levels/ requirements, schedule progression and cost projections for job completion. Manpower costing, training requirements, maintenance. Identification of required improvements to equipment and process, justification and analysis of upgrade costs through CAPEX. Review of bid documentation